High precision laser machining
Welas Oy Ltd is specialized in laser machining of metal and steel parts that are small, thin and require high precision. We design and realize closely drilled holes, openings, slits and special forms for dimensionally accurate fine mechanical parts.
We act responsibly and always focus on our function. Our company is certified according to quality and environment standards (ISO 9001: ISO 14001).
Products and Services of Laser Technology
Our services
- Design and prototypes
Expert solutions for testing, researching and manufacturing laser parts and components that are completely new or in the works.
- Serial production
A consultative manufacturing partner for making the technical realization of small, high precision components a reality.
- Contract manufacturer
A knowledgeable and flexible supplier when machining demanding and thin materials and machining components.
- Segmented Ink Blade for the Printing Industry
Segmented ink blades intended for use within the graphic industry.
Materials
Our know-how and production techniques fit the following materials exceptionally well:
- Steel (Fe)
- Stainless steel, Acid-proof steel
- Aluminium (Al)
- Copper (Cu), Nickel (Ni), Brass
- Palladium (Pd), Gold (Au), Tantalum (Ta), Tungsten (W), Noble metals
Tin bronze, Nickel silver, Silver (Ag) - Titanium (Ti), Ceramics
- Silicon (Si)
If the material needed for your project was not present on this list, please do not hesitate to contact us and we will tell you more about our possibilities and solutions.
Laser Technology
Laser machining methods offered by Welas:
- Laser Micromachining
- Laser Cutting
- Laser Welding
- Laser Drilling
- Laser Marking
We also provide bending, grinding and coating of materials as well as micro water jet cutting for heat sensitive materials.
High Precision Laser Machining
Did you know?
A laser beam can optically be very accurately focused according to fiducial marks or already present forms.
Photo Gallery
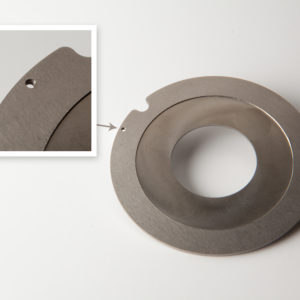
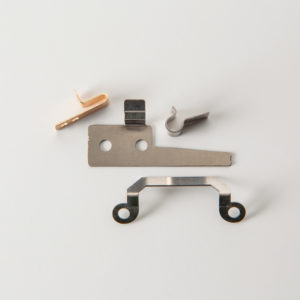
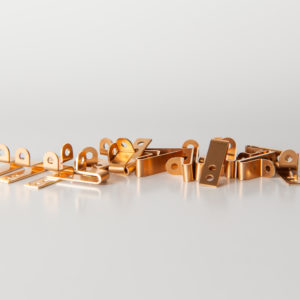
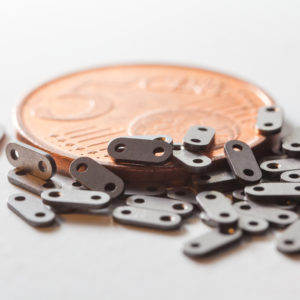
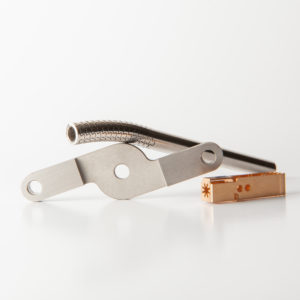
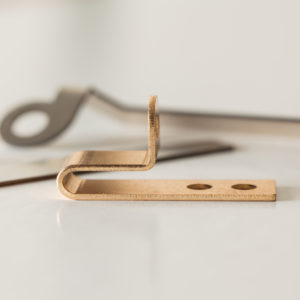
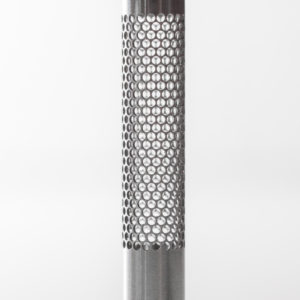
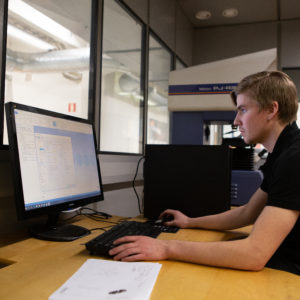